Process
Cleaning and sorting process
The process steps
-
Cleaning with air and sieves
-
Destoning
-
Screening out foreign grains
-
Surface processing
-
Air sorting
-
Grain size sorting
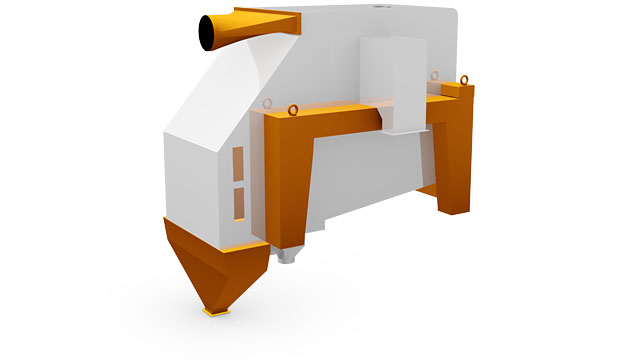
Cleaning sieve type TAS
Cleaning with air and sieves
The grain is spread over oscillating sieving decks. With the aid of suction air, dust and hulls are removed and coarse impurities are later sieved out on the pre-sieve. The primary sieve layer separates out premature grains and sand. Subsequently, the cleaned grain is once again aspirated intensively.
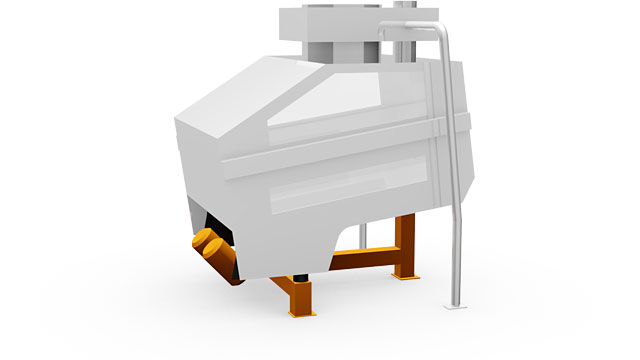
Destoner type MTSC
Destoning
On the first layer of the machine driven by vibration motors, a pre-separation takes place. Light and heavy particles are separated according to specific weight via currents of air and oscillating movements. On the second sieve layer, the separation of grain and heavy particles takes place.
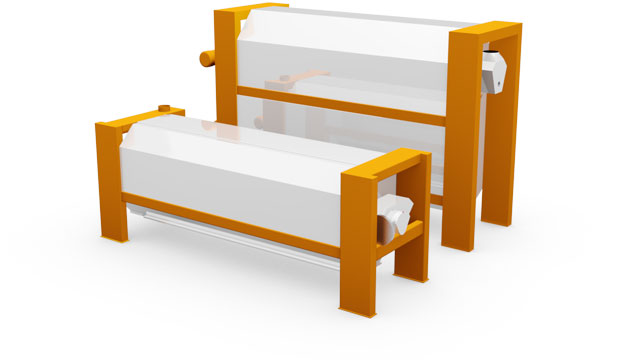
Indent cylinder type ETA
Screening out foreign grains
The screening out of weed seeds and foreign grains takes place with the aid of tear-shaped dents on the two half-shells of the working cylinder. Using a second sorting drum with a circumferential sieve, a post-sorting of the material takes place. This allows foreign grains to be reliably separated out.
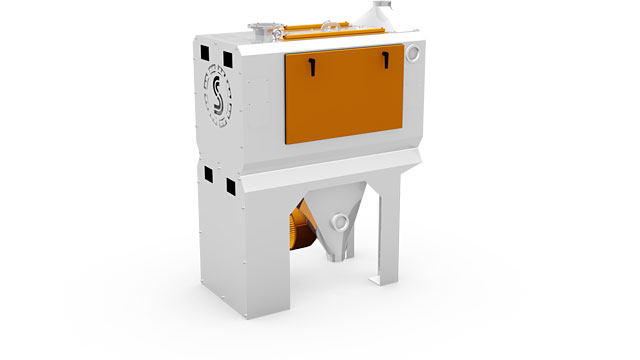
Horizontal scourer type HSM 45-80
Surface processing
The surface of the grains is polished using a horizontal special rotor. The intensity of the friction can be adjusted via various tools installed on the rotor and the outlet hatch. Subsequently, the dust generated from abrasion is extracted from the machine via suction.
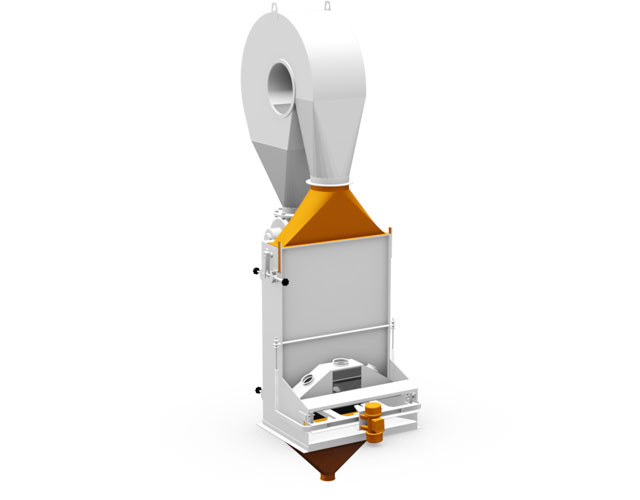
Airleg separator type STS
Air sorting
In the airleg channel, the upwards-streaming air passes through the resulting product “haze” from the grain. Here, the hulls and hull parts, which have a lighter specific weight, are pulled upwards and eliminated from the system. The heavy grain kernels flow downwards and out of the airleg separator.

Sorting cylinder type HS
Grain size sorting
The use of up to four sieves in the rotating sieve drum allows for classification into five different size grades (4 sieve size grades plus overrun). The result: Homogeneous product batches for effective further processing and the basis for a good hulling result.